In addition to mechanical recycling, chemical recycling is increasingly coming into focus for more challenging plastic streams. This article provides an overview of different recycling processes – and the challenges that arise, particularly in the area of food packaging as a result of regulations or the cost-effectiveness of the process.
How can we manage to recycle significantly more waste packaging materials, and how can we successfully drive an ecological and cost-effective circular economy for plastics? Paper, glass and even aluminum have strong reputations as recyclable materials. As far as plastic is concerned, we are still a few steps behind, because for decades, since the development of this uniquely diverse material, the focus has been on where it can be used beneficially. Designing products so that they can be recycled, or thinking about what happens when a plastic product has served its purpose and becomes waste, hardly played a role. It is only in recent years that the drive for a circular economy has gained momentum. It will only be possible to take full advantage of all the positive characteristics of plastic once the circular economy has been implemented. Because the advantages are not only limited to the variety of possible applications or the price/performance ratio.
In the meantime, the entire industry is aware of this and is bringing together its know-how and commitment to find an answer to the question at the beginning of this article. It involves the conservation of natural resources, the reduction of waste, which in many places pollutes land and water, and it is also one of the keys to the reduction of greenhouse gas emissions and, as a result, a key to fighting against climate change. Many reports from the plastics industry relate to promising pilot projects based on improved sorting and recycling processes, new products made of recycled or organic-based plastics or recyclable packaging solutions.
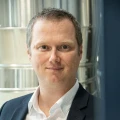
Klaus Lederer
Technology Research Manager
Chemical Recycling, EREMA Group
„In addition to the technological development of chemical recycling, it is essential for the plastics industry to gain and strengthen consumer confidence.“
Chemical Recycling as a Potential Solution for Difficult Cases?
More and more attention has recently been paid to chemical recycling as a potential solution for many particularly challenging plastic streams, especially for food packaging. In the case of PET, mechanical recycling has been very successful for many years, thanks also to Erema’s Vacurema technology. PET bottles and trays made from up to 100 % rPET meet the highest quality standards and are now increasingly the rule rather than the exception. The situation is different, however, for mechanically recycled non-PET materials. Their use in food packaging is severely restricted by the current EFSA (European Food Safety Authority) evaluation criteria. PCR plastics (except PET), produced from food packaging waste, can therefore only be returned to food packaging in a few cases in Europe, even if they have been processed completely separately. Mechanical recycling solutions with FDA (Food and Drug Administration) approval for defined input streams are available – including solutions provided by Erema – for HDPE beverage containers and for HDPE closures for HDPE, PP and PET bottles. The recyclate produced from these processes can be used in proportions of up to 100 % for food packaging.
In the EU, however, where the bar is set particularly high in terms of recycling targets, a final EFSA assessment for the recycling of HDPE food contact materials is still pending. This is one of the reasons why chemical recycling is gaining in interest. And indeed, consumers who are interested in recycling are increasingly noticing packaging with labels such as “made from xy percent certified circular polymer from post-consumer plastic” or “uses recycled plastic” on supermarket shelves. This does not mean, however, that the product the consumer is holding in their hands when they read these words actually contains recycled plastic. How can that be?
Chemical Recycling also Requires a Pre-Treated Input Stream
Mechanical recycling processes require separate treatment of the respective type of plastic if the recycled pellets are to be reused in materials with direct food contact. PET bottles, HDPE films, HDPE and PP hollow bodies, for example, are collected separately or sorted out and processed to form recycled pellets, which in turn are used to produce bottles, films or hollow bodies with a recycled content of up to 100 %. In the case of PET bottles, this cycle is traceable and transparent. The labelling on the bottle provides information about the actual proportion of recycled plastic it contains.
Chemical recycling technologies such as pyrolytic processes are capable to a certain extent, of separating mixed plastic waste materials – especially polyolefins (PO) – into their chemical components (hydrocarbons) by introducing thermal energy and, if necessary, catalysts. That is how pyrolysis oil is obtained, which can be considered like a synthetic crude oil and is composed of various fractions (including naphtha). Following appropriate pre-treatment in the refinery, plastics – mostly polyolefins – can be produced again as a result of steam cracking and polymerization, among other things. Depending on the composition and chain length, the remaining components can be used as chemicals for new products or as fuels. The quality of circular naphtha and the extent to which it can be recovered from the respective plastic waste stream for plastics production also depends on its purity and the treatment process used. The decisive factor in these processes is that foreign components such as PVC, PET and PA are not present in the PO input stream, or only in small proportions.
Transparent Labelling, But How?
Establishing separate processes for the chemical recycling of plastic to plastic by keeping each material flow separate, would require investments that are unlikely to be justified either economically or ecologically in the future. That is why chemically recycled materials are processed together with crude oil-based feedstock using existing petrochemical infrastructure (refinery, steam cracker, polymerization plants). Following this process, it is no longer possible to distinguish between original fossil chemicals and recycled materials. What is needed, is a method to determine the proportion of recycled materials obtained from chemical recycling that can be used in products such as new food packaging that can be marketed as recycled goods. To do this, the mass balance approach is used, as it is in a similar way for trading in green electricity. Figuratively speaking, just as green electricity and electricity from coal-fired or nuclear power plants flow at different rates along the same power line to arrive at the consumer’s wall socket, original fossil molecules and recycled molecules are processed in the same plants, although the products are marketed separately based on the mass balance approach. Here, too, the distribution rates can vary greatly. It would be possible, for example, for the consumer to hold in their hand packaging that actually contains 0 % recycled plastic, despite labelling to the contrary – ISCC Plus certification of the entire process chain has now become established as a reference for this. While this may sound strange at first, it does add up. Existing infrastructures can be used in a resource-saving way to further develop chemical recycling, which is still at the beginning of being industrialized.
How Material Preparation Supports the Recycling Process Chain
Erema has been behind the development of mechanical recycling over the past decades, and the company’s innovations have driven development forwards. Technological progress in chemical recycling is also supported using the experience of the Erema Group subsidiary Keycycle, both on the integration of recycling solutions into existing plants and on material preparation upstream of extrusion. Often, mechanical processes are at the beginning of the process chain for chemical recycling, in order to process post-consumer input streams and to ensure a reliable, continuous and energy-efficient material feed into the chemical recycling process, which contributes to maintaining output quality. Erema single-screw melting systems with preconditioning units (PCU) adapted to the respective requirements are already being used for this purpose at existing plants worldwide, because their technological advantages have also been proven for this application (see Info box).
By joining the Chemical Recycling Europe association, Erema wants to enhance its understanding of the needs of plant operators and promote cooperation and innovation. In order to achieve the transformation to a circular economy for plastics mentioned earlier, the technical capabilities of mechanical recycling need to be exploited to the full by expanding collection, sorting and recycling infrastructure and by further developing the technologies and end applications to be designed for recycling. For material flows where this recycling route is approaching its limits, it is important to regulate and apply additional processes. As an additional level in the recycling pyramid between mechanical material recycling and incineration with energy recovery, chemical raw material recycling is an addition that makes sense in the long term to keep a maximum of raw materials within the circular economy.
In addition to the technological development of chemical recycling and the implementation of the first industrial-scale plants, it is essential for the plastics industry as a whole to gain and strengthen consumer confidence. Plastic is not only the most versatile material, but also the most environmentally friendly in many areas of application when the entire life cycle is considered objectively. Transparent communication about the recycling process end-to-end, as well as certification and product labeling, are essential to close the loop and ensure that the potential of plastics as part of the solution for environmental and climate protection is appreciated by consumers and can be utilized to the full.
© Carl Hanser Verlag, München, Kunststoffe 1/2022